Power quality assessment is crucial for commercial and industrial environments due to the following reasons:
1. Equipment Sensitivity:
- Commercial and industrial facilities often use sensitive electronic equipment and machinery. Power quality issues, such as voltage fluctuations, harmonic distortions, and interruptions, can adversely affect the performance and reliability of these devices.
2. Production Efficiency:
- In industrial settings, even minor disruptions in power quality can lead to production inefficiencies and downtime. Power quality assessments help identify and rectify issues that could impact the smooth operation of manufacturing processes.
3. Equipment Longevity:
- Industrial equipment is often expensive and designed for a specific operational environment. Poor power quality can lead to premature aging and failure of equipment, resulting in costly replacements. Regular assessments help extend the lifespan of machinery and reduce the overall cost of ownership.
4. Data Integrity:
- Many commercial and industrial processes rely on computer systems for data collection, monitoring, and control. Power quality issues can lead to data corruption, loss, or system failures. Assessments ensure the reliability and integrity of data, which is crucial for decision-making and quality control.
5. Compliance with Standards:
- Commercial and industrial facilities are subject to various standards and regulations related to power quality. Compliance with these standards is essential to avoid penalties, legal issues, and to maintain a safe working environment.
6. Energy Efficiency:
- Poor power quality can result in energy wastage and increased operational costs. By identifying and rectifying power quality issues, commercial and industrial facilities can improve energy efficiency, leading to cost savings over time.
7. Financial Impact:
- Downtime and equipment failures in commercial and industrial environments can have significant financial implications. Power quality assessments help prevent such issues, ensuring continuous and reliable operation.
8. Improved Equipment Performance:
- Power quality assessments can identify and address issues that might degrade the performance of sensitive equipment. This leads to consistent and reliable performance, ensuring that equipment operates at its designed capacity.
9. Diagnostic Capability:
- Power quality monitoring provides valuable data for diagnosing the root causes of issues. This information is essential for implementing targeted solutions and preventing recurring problems.
10. Insurance and Liability:
- Insurance providers may require proof of power quality measures to mitigate risks associated with equipment damage or business interruption. Assessments help in providing evidence of proactive measures, potentially reducing insurance premiums.
11. Proactive Problem Identification:
- Regular assessments provide a proactive approach to identify potential power quality issues before they escalate. This allows for timely corrective measures, preventing more extensive problems and minimizing the need for emergency repairs.
12. Cost Savings:
- By preventing equipment failures, reducing downtime, and improving energy efficiency, power quality assessments contribute to overall cost savings for businesses. This includes savings on repair and maintenance costs and potential insurance premium reductions.
In summary,
power quality assessment
is essential for commercial and industrial environments to ensure the reliable and efficient operation of equipment, maintain compliance with standards, and mitigate financial and operational risks. It is a proactive approach that contributes to the overall success and sustainability of businesses in these sectors.
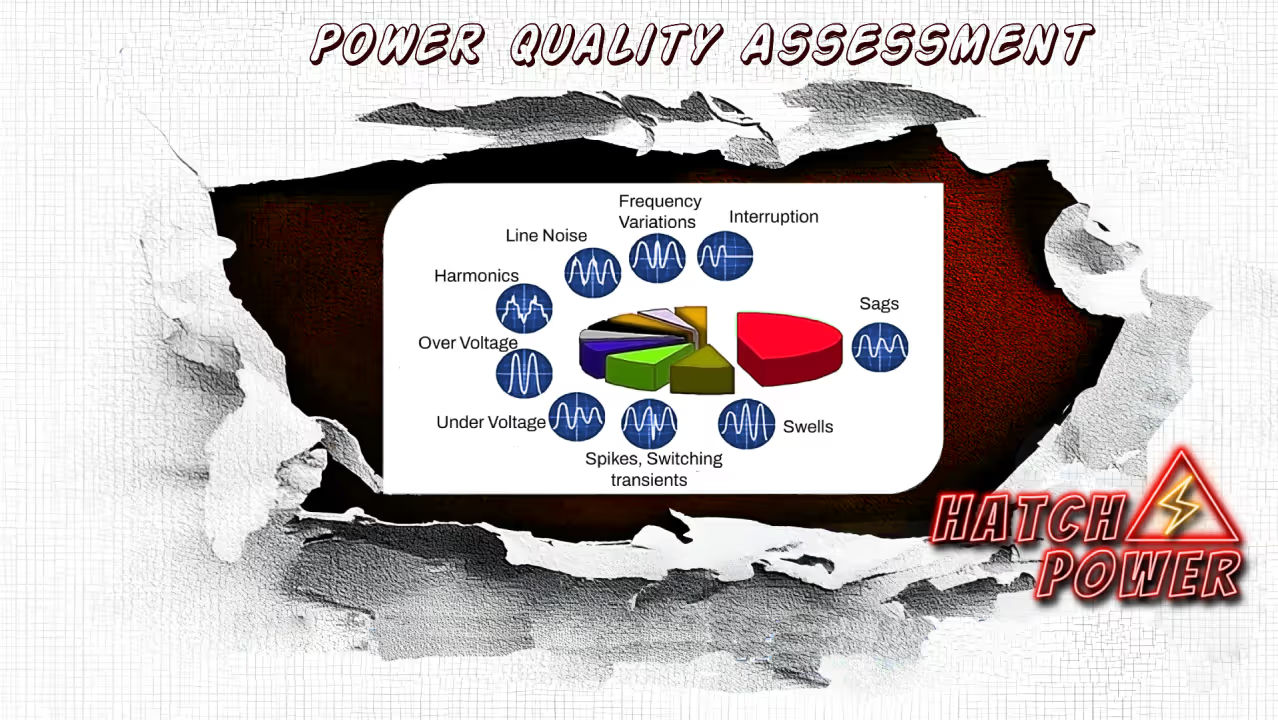