Introduction:
The manufacturing plant operated various heavy machinery and automated production lines. The plant relied on a UPS system to protect critical control systems, electronic equipment, and maintain uninterrupted production during power disruptions.
This case study examines an incident where a UPS systems failure occurred in this manufacturing plant due to an un-calibrated UPS system. The failure resulted in a critical production line shutdown, leading to extensive downtime, production losses, and financial impact on the company.
Incident Details:
After business hours, the plant's management decided to conduct major preventive maintenance on the UPS systems to ensure their optimal performance. However, due to time constraints and a lack of clear procedures, the major PM, including the calibration process, was rushed and not completed as intended.
A few weeks later, there was a momentary failure in UPS operation.
Root Cause Analysis:
1- The primary cause of the UPS systems failure was the incomplete calibration process carried out during the maintenance window. the calibration process was rushed, leading to inaccuracies and misalignment in the UPS system's settings. while the Calibration is essential to ensure that the UPS system operates accurately within specified tolerances.
2- The plant did not conduct comprehensive testing after the calibration process to verify the UPS system's functionality under real-world conditions.
Impacts:
1- Production Downtime: The critical power outage caused by the UPS systems failure resulted in a complete shutdown of the production lines, leading to significant downtime.
2- Production Losses: The downtime caused by the UPS systems failure resulted in production losses, delayed orders, and decreased productivity, impacting the company's revenue.
3- Equipment Damage: The abrupt power disruption caused by the UPS systems failure led to potential damage to some connected machinery and electronic equipment.
4- Financial Impact: The combination of production losses, equipment damage, and recovery efforts incurred significant financial losses for the manufacturing plant.
Lessons Learned:
1- Comprehensive Calibration: Allocate sufficient time and resources to carry out a thorough calibration process for UPS systems.
2- Clear Procedures: Performing detailed calibration procedures recommended by the UPS manufacturer and ensuring that they are well-documented and easily accessible to maintenance personnel
3- Testing and Validation: Conduct comprehensive testing and validation of UPS systems after calibration to verify their functionality under real-world conditions.
4- Preventive Maintenance: Implement a proactive preventive maintenance schedule, including regular calibration checks, to ensure the UPS systems' optimal performance.
Conclusion:
The UPS systems failure due to an un-calibrated UPS system emphasizes the significance of accurate calibration and testing in critical power infrastructure management. By prioritizing proper calibration procedures, documentation, and comprehensive testing, organizations can prevent UPS failures, minimize downtime, and avoid costly repercussions on their operations and financial health.
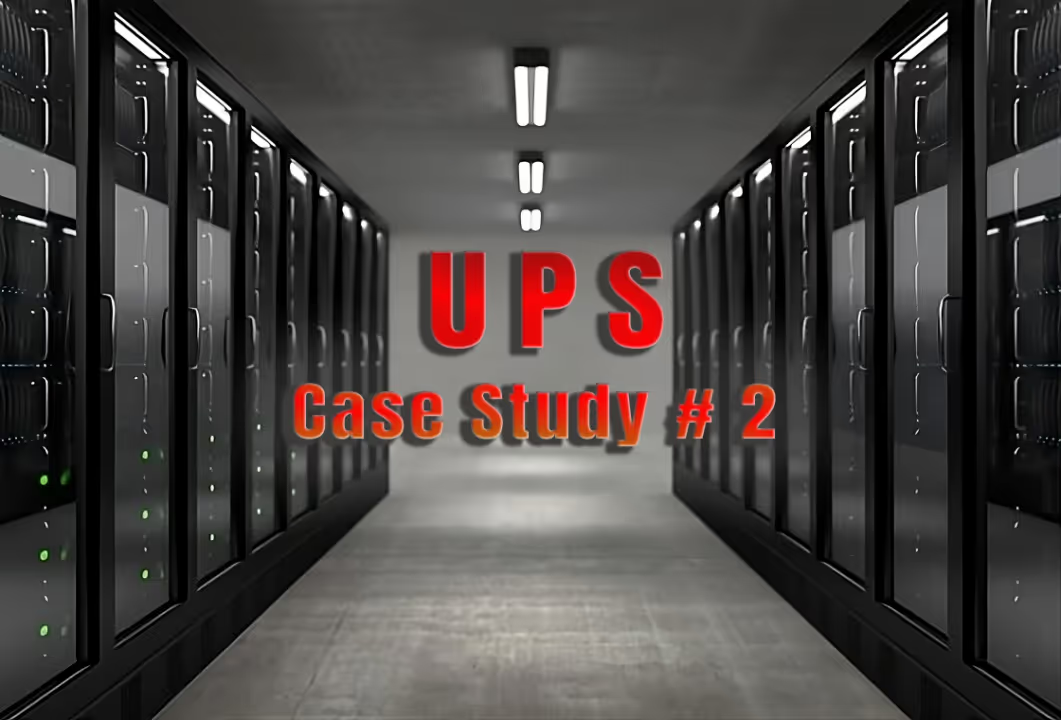